Twenty-First Century Mosaics
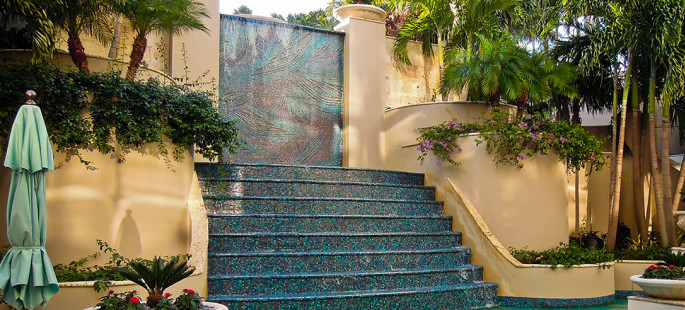
Artaic designs and assembles custom mosaics. Any source image – a rendering, photograph, art print, magazine cut-out, etc. – can be converted into a mosaic of any size. The process involves computer-aided design software, a team of artists working directly with clients, and four robots which precisely assemble the tiles into 1 sq. ft. sections. The sections are labeled and shipped as a kit for installation by local professionals.
Since launching in 2007, Artaic has completed projects for big-name clients in the hospitality, retail, nonprofit, higher education, and medical sectors including Ritz-Carlton, Hilton, MGM Resorts International, Walt Disney World, Saks Fifth Avenue, and Saint Elizabeth’s Medical Center.
As Artaic grew, it became difficult to manage the vast inventory of tiles of varying size, color, and finish. With shipping costs mounting, Acworth sought a solution to Artaic’s problems at UMass Amherst.
Managing the supply chain was a difficult challenge as our mosaics are custom made on demand. They are highly customizable pieces of art, and each requires different tiles of various materials, colors and finishes. It’s not like a printer where you just need to order ink. These tiles come from all over the world, and it’s difficult to determine what people may want in advance,” said Acworth. “There’s not a lot of theory on this subject, so we approached UMass Amherst to collaborate on original research.”
According to Muriel, Artaic’s issues were rooted in their supply chain and logistics. Tile shipments often came by air in frequent, small shipments as clients commissioned projects. This resulted in shipping costs nearly equal to the cost of the tile. If there was a way to predict how many tiles they would need of each specific color, finish, and size, Artaic could reduce shipping costs by placing larger orders and shipping mainly by ocean just four times a year.
“We figured out a way to coordinate all of the different tile SKUs, so they could be ocean shipped,” said Muriel. “There is tremendous uncertainty because of the customized nature of mosaics. It’s difficult to determine how many bright red tiles, for example, you will need to complete future orders. Further, in this industry, everything needs to be ordered in 22lbs, 44lbs, or 66lbs boxes. That presents an additional logistical challenge. It’s not something that has been done before.”
Muriel and her students developed an algorithm to help Artaic determine which tiles to order on a quarterly basis. By analyzing current inventory, historical demand for various tiles, and projects in the pipeline, this new tool can accurately predict how many of each of the numerous colors and finishes the company should order. This allows Artaic to cut shipping costs by roughly $50,000 a shipment, improve customer responsiveness, and ensure correct inventory for current and future projects.
“Not only do we save on shipping costs and cut lead times, but we also ship in a much more environmentally conscious way. I purchase whatever I can find domestically. For international procurements, it’s much better to consolidate inventory shipments into fewer larger ocean freight shipments,” said Acworth. “I hate burning jet fuel to fly tile.”
The results have been promising for Muriel’s research group as well. Their work was recognized at the 2017 Institute of Industrial and Systems Engineers Conference with an award for Best Track Paper in Logistics and Supply Chain.
With this problem solved, Muriel began work on the second phase of her collaboration with Artaic – a new algorithm to predict project completion times for clients.
“We work with many clients in industries on tight timetables, often in the midst of large construction projects. If a client is building a hotel or hospital, or a university is renovating an athletic facility, the order needs to be done yesterday. It is crucial that we give clients an accurate timeline,” said Acworth.
The algorithm Muriel and her students are currently developing analyzes completed projects and projects in the pipeline to predict lead times. Once completed, it will allow sales representatives to instantly give customers accurate information on project cost and lead time.
The collaboration between Artaic and UMass Amherst serves as an example of a mutually beneficial partnership between university and industry. While Artaic has reduced shipping costs, lowered lead times, and increased financial gains, students have gained real-world experience with an innovative Massachusetts business.
“Small businesses have a harder time collaborating with large research universities on research. Big corporations can easily fund projects, but we have much less money and time. It’s daunting for small businesses to begin such a partnership, but our work with UMass Amherst has been invaluable to the company,” said Acworth. “It’s been very easy to collaborate with UMass Amherst, and it’s resulted in immense value for my company.”
“My major motivation for working with companies like Artaic is the engagement it brings students,” said Muriel. “They are able to work on real-world problems and see the results their solutions have on companies. They are much more motivated when they apply their research and classroom instruction to actual companies. Businesses see this as an opportunity for groundbreaking research and to meet the students who will be filling positions within their companies.”
“Our mission is to work collaboratively with industry to advance the fields of design and manufacturing. Ted is very forward-looking, and Artaic is the kind of disruptive company that we want to partner with,” said Sundar Krishnamurty, head of the Mechanical and Industrial Engineering Department and director of the Center for e-Design. “These projects speak to who we are as a public research university, and how we value industry relationships.”
Since 2014, $116,000 in direct National Science Foundation funding and $65,000 in-kind support from UMass Amherst has supported Muriel, nine undergraduate students, and 2 PhD students in their research partnership with Artaic.